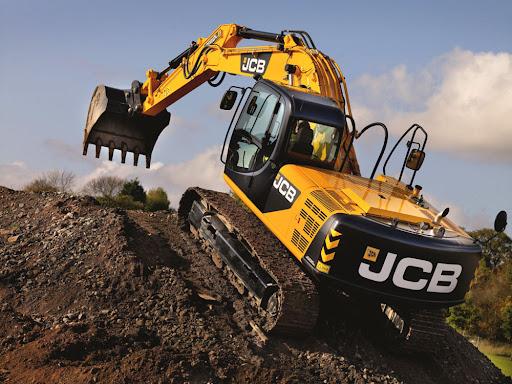
Regular maintenance combined with proper machine operation greatly reduces track wear, improves efficiency and lowers operating costs.
Product Manager for earthmoving tools, excavator tracks and other undercarriage components at Volvo CE EMEA, states, “Proper track maintenance is important for the overall service life of heavy machinery. Poorly maintained wear parts shorten the life of the machine and increase the risk of breakdowns and unplanned downtime.” . And consequently additional costs and lost profits.
Crawler excavators have a robust steel structure, for which reason track maintenance is often neglected, which in turn can be a costly mistake.
“Studies show that repair costs for the undercarriage of a crawler excavator account for 40-60% of the total repair costs over the life of the machine. A worn undercarriage increases the excavator’s vibration level, which shortens the life of the pump, engine and electronics.”
There are several signs that the excavator tracks are not receiving enough attention. Typical signs of poor track maintenance are:
- Stretching of the track (which indicates wear on the pin);
- Reduced component life;
- Unusual wear pattern;
- Increased frequency of failures.
- So, what proper maintenance of the excavator track entails and how to extend component life, you will learn in this article!
Tip #1. Check the track tension
Improper track tension or “track slack” is a major cause of accelerated component wear. Excessive tensioning increases friction between components, causing the track to wear. Insufficient tensioning increases pitch and there is a risk of losing parts.
Check the excavator track tension in suitable conditions (hard, dry surface), then follow the recommendations for track adjustment in the manufacturer’s manual.
“Check the tension regularly, especially when changing work area locations, as different materials underfoot affect the tension of the track in different ways.”
In addition to track tensioning, it is important to bear in mind that when replacing any part of the track system, you should check the wear of the associated components. A worn sprocket, for example, can shorten the life of the new chain.
Tip No 2. Don’t ignore the basic rules for handling heavy machinery
Environmental conditions and situations vary, but there are management rules that increase component life:
- Turn machinery in a wide arc. Sharp turns accelerate the wear of the excavator track.
- Avoid adverse environmental conditions: rough asphalt, concrete and other abrasive materials that damage the track.
- Choose the correct shoe width: considering the weight of the machine and the environment in which it is used. Narrow excavator shoes are suitable for hard surfaces, providing better grip on the ground. Wide shoe widths are suitable for soft surfaces as they have greater floatation with lower ground pressure.
- Choose the right traction shoe: Consider the working environment before selecting the number of components. The more grousers on the track, the more contact with the surface and the less vibration.
- Drivers should avoid travelling long distances at high speeds. High speeds increase the stress between the components, causing wear on the undercarriage. Over long distances, friction increases causing heat to build up in the rollers, wheel guides and drive train, damaging the internal seals.
In addition to maintenance, driver performance is one of the most important factors in component life. The inexperienced driver assumes that the undercarriage is designed to run on ‘everything’, including rocks and mouldboards. But, this is a costly mistake!
Tip #3: Use rubber tracks for sensitive surfaces
Rubber tracks are available on small excavators. In particular, the components provide passability by enabling excavators to travel on soft ground. Rubber tracks have minimal impact on the surface of the finished area.
You should begin operating the equipment by visually inspecting it for wear and dirt. It is helpful to avoid:
- Rolling of the tracks;
- High speed;
- Driving in reverse.
Tip #4. Keep the track clean
At the end of the work day, excavator drivers should take time to remove dirt and other debris that accumulates during the shift. Regardless of the application, if the track is dirty, it must be cleaned. Ignoring this factor leads to premature component wear.
When drivers neglect to clean the track in winter, dirt and debris freeze. Once this happens, the material begins to rub against the bolts, loosen the guide wheel, and the rollers get jammed, further leading to wear and tear.
In addition, the debris adds weight to the excavator, which increases fuel consumption. Use small shovels and high-pressure washers to clean the track.
“Leaving the track dirty is a costly mistake. Dirt gets on the pins, bushings and rollers and causes excessive wear.”
Tip #5. Check the excavator track regularly
It is important to perform a complete inspection of the components for excessive or uneven wear, and to look for damaged or missing components. If the machine is operated in severe conditions frequent inspections of the track may be necessary.
Drivers should check the track during a standard bypass inspection to ensure that components are in their proper place. If components are missing, the track is not secured properly or the track pin is damaged.
Oil leaks indicate a faulty seal that leads to failure of the rollers, guide wheels.
“Follow the manufacturer’s operating and maintenance recommendations for proper track maintenance.”
It is important to consider the total number of hours spent driving and operating the attachment in high and low speed mode. Equipment manufacturers recommend that the undercarriage be inspected and serviced every 1,000 hours of operation.